California Research Lab Insulation Options: Cost, Pros & Cons
5/12/2024 9:00 AM
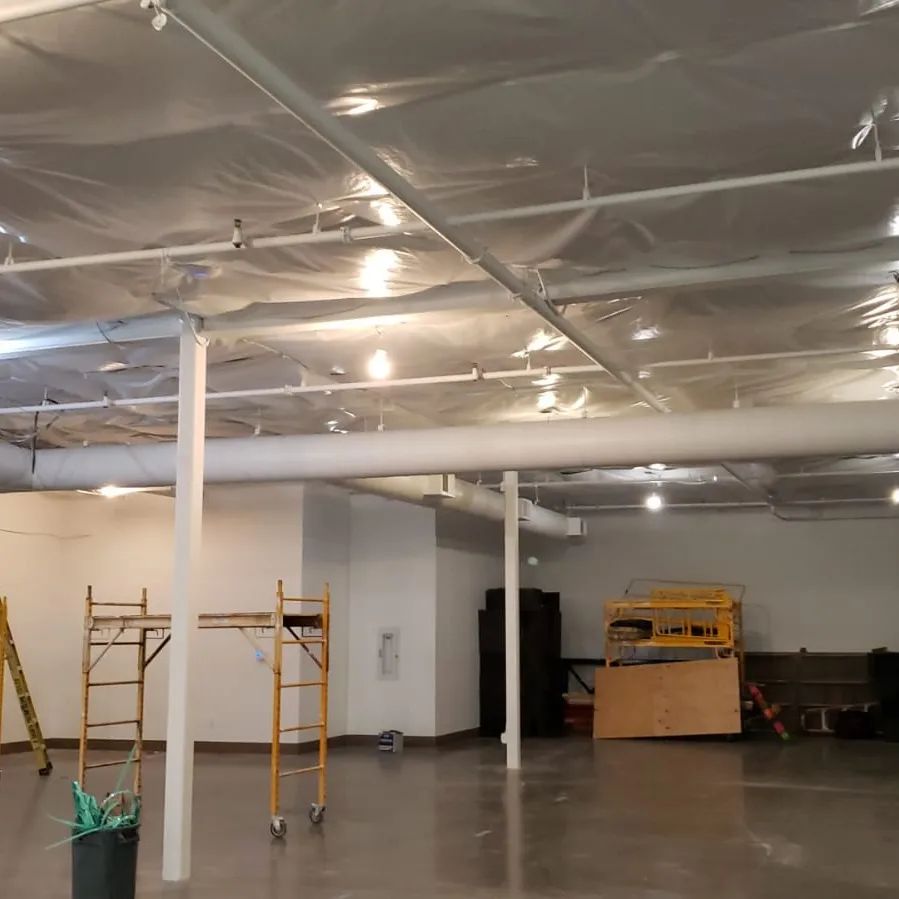
California Research Lab Insulation Options: Cost, Pros & Cons
Key Takeaways
-
Insulation materials like fiberglass, cellulose, and spray foam help California research labs maintain precise environmental conditions while managing costs.
-
Spray foam insulation offers superior thermal resistance and air sealing but has higher upfront costs ranging from $2.00 to $9.00 per square foot.
-
Fiberglass insulation is a cost-effective option at $1.40 to $3.00 per square foot, offering moderate thermal resistance but requiring more frequent replacement.
-
Eco-friendly cellulose insulation improves energy efficiency and promotes sustainability goals.
-
USA Spray Me brings over 10 years of experience providing tailored insulation solutions to improve energy efficiency and safety in California research labs.
Research Lab Insulation Options in California
Common insulation materials include fiberglass, cellulose, and spray foam, which have distinct thermal properties and cost considerations.
For instance, fiberglass insulation is widely used due to its affordability and ease of installation, while spray foam provides superior air sealing and higher R-values but at a higher cost.
USA Spray Me is an insulation company based in San Francisco and serving Northern California. Our expert technicians specialize in the application of high-quality foam polyurethane insulation, known for its superior thermal performance and air-sealing properties.
Get a Quote for Your ProjectSpray Foam Insulation
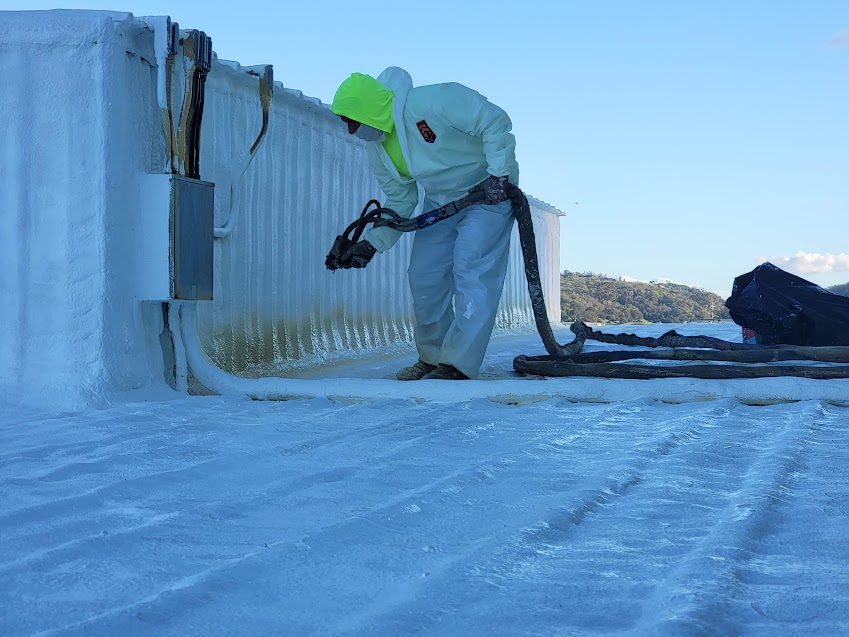
Spray foam insulation provides unmatched thermal performance for California research facilities.
Spray foam insulation provides superior thermal resistance with its high R-value. It seals gaps and air leaks effectively - ideal for labs requiring strict temperature control.
Cost Considerations
-
Cost: $2.00 to $9.00 per square foot
-
High initial cost, but long-term energy savings and durability make it cost-effective.
Advantages and Disadvantages
Advantages |
Disadvantages |
---|---|
Airtight seal for precise environmental control |
Higher upfront cost compared to other options |
Acts as a moisture barrier, preventing mold and mildew |
Requires professional installation |
Long-lasting with minimal maintenance |
Difficult to remove for future modifications |
Fiberglass Insulation
Fiberglass insulation is an affordable, widely used option for labs. Available in batts or loose-fill forms, it provides moderate thermal resistance and is easy to install.
Cost Considerations
-
Cost: $1.40 to $3.00 per square foot
-
Low cost, but shorter lifespan may require replacements over time.
Advantages and Disadvantages
Advantages |
Disadvantages |
---|---|
Affordable and widely available |
Provides less air sealing compared to spray foam |
Non-flammable and moisture-resistant |
Fibers can pose health risks during installation |
Simple to install, reducing labor costs |
Susceptible to absorbing moisture over time |
Blown-In Insulation
Blown-in insulation adapts well to irregular spaces for comprehensive coverage and flexible applications.
Cost Considerations
-
Cost: $1.50 to $4.00 per square foot
-
Affordable for retrofits and small-scale projects, but proper installation is essential.
Advantages and Disadvantages
Advantages |
Disadvantages |
---|---|
Fits irregular spaces with ease |
Requires professional installation |
Offers moderate thermal resistance |
Can settle over time, reducing effectiveness |
Polyurethane Foam Insulation
Polyurethane foam insulation is a specialized spray foam with high thermal resistance and superior air-sealing properties. It is ideal for research labs requiring precise environmental control and energy efficiency.
Cost Considerations
-
Cost: $2.00 to $9.00 per square foot
-
Higher cost, but provides excellent energy efficiency and durability.
Advantages and Disadvantages
Advantages |
Disadvantages |
---|---|
Exceptional thermal resistance and air sealing |
Higher cost |
Long lifespan with minimal maintenance |
Professional installation required |
Factors Influencing Insulation Choice
Aside from budget, environmental impact and your unique requirements will influence the choice.
Eco-friendly options like cellulose help reduce a lab’s carbon footprint and contribute to broader sustainability objectives.
The nature of the research, the equipment utilized, and the lab’s geographical location dictate the most suitable insulation type.
-
Labs conducting sensitive experiments might need insulation with excellent soundproofing to avoid noise disruptions.
-
Facilities in humid regions often require moisture-resistant insulation to safeguard equipment and ensure accurate experimental conditions.
Why Choose USA Spray Me for Your Research Lab Insulation Project
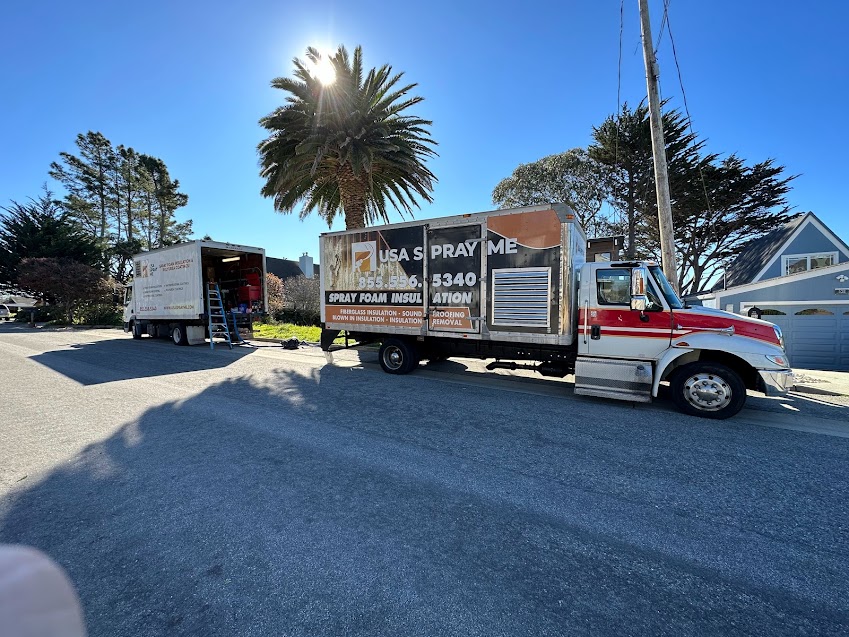
USA Spray Me delivers expert insulation services tailored to research labs in California.
At USA Spray Me, we specialize in insulation solutions designed to meet the unique demands of California research laboratories. With over 10 years of industry experience, we understand the critical need for precision in temperature control, humidity regulation, and energy efficiency—factors essential for maintaining accurate research environments.
We offer advanced insulation options like spray foam for superior thermal resistance and fiberglass for cost-effective performance. We tailor every project to the lab’s specific needs, considering factors such as sensitive equipment, noise control, and compliance with California's stringent safety and building codes.
Frequently Asked Questions (FAQ)
Here you'll find answers to the questions we get asked by our clients.
Fiberglass insulation is typically the most affordable, costing $1.40 to $3.00 per square foot. It provides decent thermal resistance but may require more frequent replacements compared to other materials like spray foam.
Spray foam insulation can last up to 80 years with proper installation and maintenance.
While fiberglass is moisture-resistant, it is not waterproof. Proper installation and the use of additional moisture barriers are needed in humid environments to prevent mold and water damage.
With good thermal performance and reduced air infiltration, cellulose insulation improves energy efficiency.
No, spray foam insulation is challenging to remove once applied - professional assistance is recommended for both application and removal.
Both insulation types offer soundproofing benefits, but spray foam is generally more effective due to its density and ability to completely fill gaps. Blown-in insulation still provides sound absorption, particularly in attics and walls, but spray foam offers better overall soundproofing.
In colder climates, spray foam’s superior air sealing and insulation properties make it a preferred choice for maximizing energy efficiency. In milder climates, blown-in insulation can provide adequate thermal resistance at a lower cost.
Many local governments and utility companies offer incentives for insulation upgrades, such as tax credits, rebates, or low-interest loans. These programs aim to promote energy efficiency improvements and reduce overall energy consumption.